American Machinist, May 2006
Download Shop Sends Manual Labor Down the Tubes PDF.
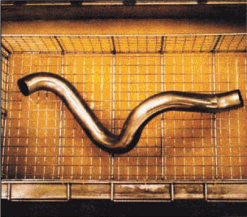
Customers of Eaton Aerospace (www.aerospase.eaton.com) in Jackson, Mich., are quite fussy about how the tubing produced by the shop looks. The tubing goes into aircraft such as the Airbus 380, the F-22 Raptor and F-35 Joint Strike Fighter to convey air, oil, water and Freon. Besides being properly machined and meeting internal quality standards, tubing must be well cleaned. Eaton relies on ultrasonic cleaning systems.
Eaton’s ultrasonic systems eliminate five to ten minutes of hand labor per tube produced. Multiplied by the facility’s output, That translates into 20 hours of saved labor weekly. “Our plant can’t afford to be slowed down or stopped, and prior to the ultrasonic systems, we cleaned tubes manually,” says Bud Greener, manufacturing engineer at Eaton. “Now, we put them (tubes) into the cleaning systems, adjust the settings and walk away to do something else while the parts are being cleaned.”
The shop runs Super Pro and Pro Plus ultrasonic cleaning systems from Omegasonics (Omegasonics.com) and two European-made ultrasonic machines that Omegasonics retrofitted with its own components. The Super Pro and Pro Plus units ride on wheels for maximum flexibility in placement and shop layout at Eaton.
For many years, Greener and his team cleaned tubing with mineral spirits and Stoddard solvent. Runoff went into a filtered tank that a contractor would rotate because Stoddard solvent is a petroleum mixture and requires special storage, usage and disposal considerations. The Omegasonics systems are environmentally friendly. Their baskets easily accommodate Eaton’s odd-shaped and small items and they thoroughly clean tubing inside and out in a hands-off process.
Eaton bends raw stainless steel tubing ranging in size from 0.750 to 3.00 in. in diameter into complex shapes. The shop cuts tube sections to length and bends them with a mandrel, a lubricated tool inserted into the tubing that prevents kinking. Post-bending cleaning is mandatory to remove processing oils and tube-bending lubricants.
Because Eaton’s output includes oversized bent tubes, it also uses two, previously purchased, European stationary ultrasonic machines with large-capacity tanks. When the internal components of these units had to be replaced, Eaton brought the systems back to life. It installed six Omegasonics transducer and generator sets per tank and built new control panels for the units.