Production Parts Aren’t Truly Finished Until They’re Ultrasonically Cleaned
In high-volume manufacturing, producing the part is only half the job — the other half is ensuring it’s impeccably clean. Residual oils, dust, handling grime, and microscopic contaminants can compromise performance, interfere with coatings, or cause failures down the line. Threads, blind holes, and complex geometries require more than surface-level cleaning.
Ultrasonic cleaning reaches where other methods can’t — penetrating every crevice to remove contaminants at a microscopic level. Whether parts are destined for assembly, coating, sterilization, or direct use, ultrasonic cleaning ensures they meet the highest standards of cleanliness, quality, and performance.
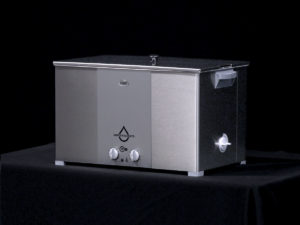
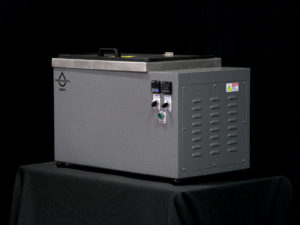
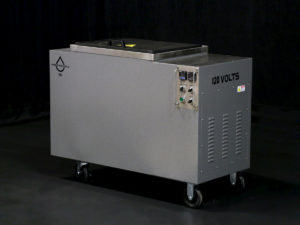
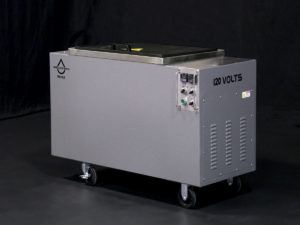
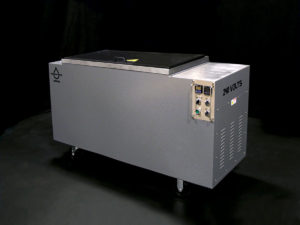
Ultrasonic cleaning is especially valuable for today’s intricate, high-precision production components. As designs become more complex and tolerances tighter, traditional cleaning methods often fall short — missing residues lodged in tiny channels, undercuts, or internal passages. Ultrasonic technology uses high-frequency sound waves and cavitation to remove contaminants from even the most inaccessible areas without damaging delicate surfaces or finishes. This makes it ideal for parts with tight geometries, fine threads, and sensitive coatings.
In addition to performance, ultrasonic cleaning adds efficiency and consistency to your production workflow. Automated or semi-automated systems allow for batch processing of hundreds of parts at once, reducing labor and turnaround time while ensuring repeatable, reliable results every cycle. It’s a cost-effective solution that improves product quality, reduces scrap rates, and supports compliance with industry cleanliness standards — making it an essential part of any modern manufacturing operation.
Features
Our clients get the highest-quality results for their money.
- In-house cleaning technology that is faster, safer and more cost-effective
- No employee training required
- Uses only safe, chemical-free solutions
- Removes metal shavings, coolant, oil, dust, calcium, carbon, dirt and grime from invisible surfaces or crevices unreachable by brushes, picks or rags
- No risk of recontamination
Case Study
Learn how Pacific Consolidated, largest dedicated provider of additive manufacturing/3D printing, rapid prototyping, tooling and injection molding services in U.S. made the switch to ultrasonic cleaning.